Dry Sorbent Injection System (DSI) in Pune, India: Stratgem

In simple words, The DSI system removes metals (Hg, and so on), volatile organic
compounds
(VOCs), and acid gases (SO₂, SO₃/H₂SO₄, HCl) by injecting calcium- or sodium-based
alkaline
sorbents into the flue gas.
Dry Sorbent Injection System Process Diagram:
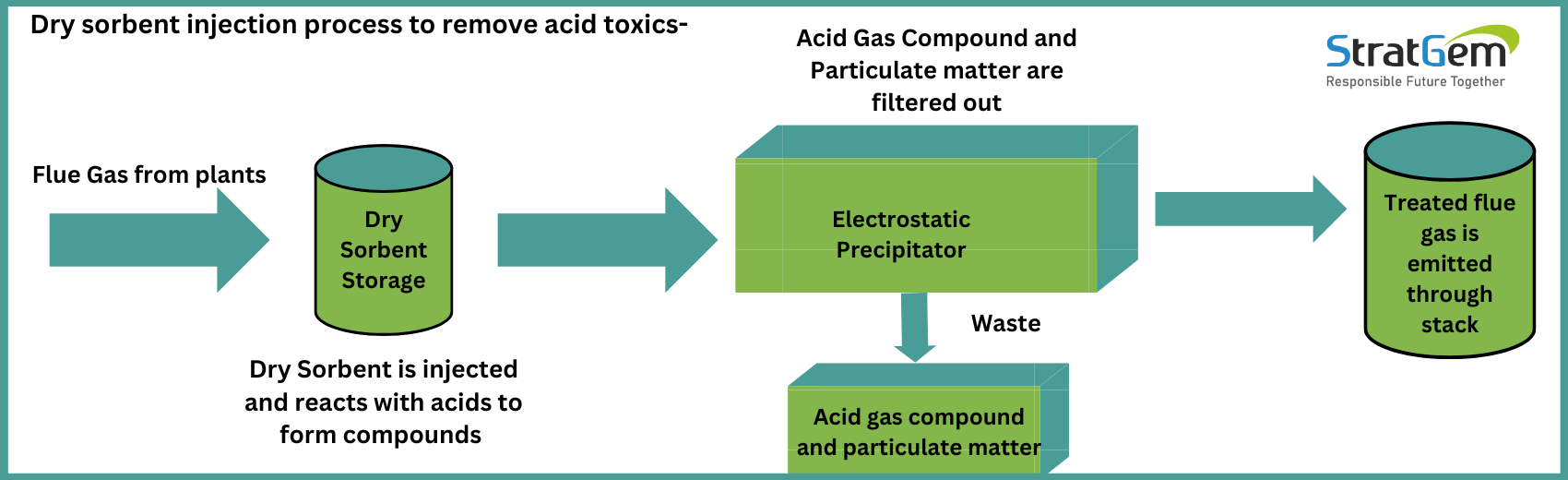
- Flue Gas Stream Collection: The process begins with the collection of the flue gas stream from the industrial process, such as a coal-fired power plant or waste incinerator. The flue gas contains pollutants such as sulfur dioxide (SO2) and hydrogen chloride (HCl), which need to be controlled to meet regulatory requirements.
- Sorbent Preparation: Dry sorbents, such as lime (calcium hydroxide) or sodium bicarbonate, are prepared for injection into the flue gas stream. The sorbents are typically stored in silos and may undergo grinding or milling to achieve the desired particle size distribution before injection.
- Injection of Sorbents: The prepared dry sorbents are injected into the flue gas stream at a controlled rate and location downstream of the combustion process. Injection methods can vary but commonly involve pneumatic conveying systems or specialized injection nozzles to introduce the sorbents into the flue gas.
- Mixing and Reaction:As the sorbent particles mix with the hot flue gas, chemical reactions occur between the sorbents and acidic gases present in the flue gas stream. For example, lime reacts with sulfur dioxide to form calcium sulfite or calcium depending on the conditions. These reactions neutralize the acidic gases, converting them into less harmful compounds.
- Particle Capture: The reaction products, along with any unreacted sorbent particles, form solid particulates within the flue gas stream. These particles are then captured by downstream particulate control devices, such as electrostatic precipitators (ESPs) or fabric filters (baghouses). These devices efficiently remove the solid particulates from the flue gas stream, ensuring compliance with emission regulations.
- Residual Handling: The captured solids, which contain the reacted sorbent and reaction products, are collected and typically disposed of or reused. Depending on the composition and regulations, these residuals may be landfilled, recycled for other industrial processes, or utilized in beneficial applications such as construction materials.
- Monitoring and Control: Throughout the operation of the DSI system, various parameters such as sorbent injection rate, flue gas temperature, and pollutant concentrations are monitored and controlled to optimize performance and ensure compliance with emission limits.
Benefits of Dry Sorbent Injection System:
- Cost-Effective: DSI systems are often more cost-effective compared to other pollution control technologies like wet scrubbers. They typically have lower capital and operational costs, making them attractive for industries looking to reduce emissions without breaking the bank.
- Easy Installation and Retrofitting: DSI systems can be relatively easy to install, and they can often be retrofitted onto existing infrastructure without requiring significant modifications. This ease of installation makes DSI a practical option for industries looking to quickly improve their environmental performance.
- Versatility: DSI systems can be used to control a wide range of pollutants, including sulfur dioxide (SO2), hydrogen chloride (HCl), sulfur trioxide (SO3), mercury, and other acid gases. This versatility makes DSI a flexible solution for industries facing multiple emission challenges.
- Reduced Water Usage: Unlike wet scrubbers, which require large amounts of water for the scrubbing process, DSI systems operate without using water. This can be advantageous in areas where water availability or disposal is a concern, and it also eliminates the need for wastewater treatment facilities.
- Minimal Waste Generation: DSI systems typically generate minimal waste compared to wet scrubbers, which produce a liquid waste stream that requires treatment and disposal. With DSI, the sorbent and captured pollutants can often be disposed of or recycled in a more straightforward manner.
- High Removal Efficiency: When properly designed and operated, DSI systems can achieve high removal efficiencies for targeted pollutants, helping industries meet regulatory requirements and improve their environmental stewardship.
- Minimal Maintenance Requirements: DSI systems typically have lower maintenance requirements compared to wet scrubbers, as they don't involve complex liquid-handling systems prone to corrosion and scaling. This can result in reduced downtime and lower operating costs over the long term.
Application OF Dry Sorbent Injection System in Industries:
- Coal-fired Power Plants: Coal-fired power plants are one of the largest emitters of SO2 and other pollutants. DSI systems can be used to inject dry alkaline sorbents such as lime (calcium oxide) or sodium bicarbonate into the flue gas stream to neutralize acidic gases and reduce SO2 emissions.
- Waste-to-Energy Plants: DSI can be employed to mitigate emissions by injecting sorbents into the flue gas stream, thus reducing the release of pollutants into the atmosphere.
- Cement Plants: Cement manufacturing involves high-temperature processes that can generate significant amounts of SO2 and other pollutants. DSI systems can be installed in cement plants to capture and neutralize these emissions before they are released into the atmosphere.
- Refineries and Petrochemical Plants: Refineries and petrochemical plants produce sulfur-containing gases and other pollutants during various refining processes. DSI can be used to control emissions by injecting sorbents into flue gas streams, thereby reducing the environmental impact of these facilities.
Overall, DSI is a versatile technology that offers an effective means of reducing
emissions of
acidic gases and heavy metals across a wide range of industrial processes, helping
to improve
air quality and comply with environmental regulations.
Stratgem develops and manufactures Dry Sorbent Injection Systems based on the needs
and
specifications of the customer for the product.
Stratgem Pune, India offers comprehensive services such as field service, start-up
service,
full-scale material testing, and spare parts. Among the industries we serve are
food,
chemicals, pharmaceuticals, plastics, minerals, and others. To know more about the
Dry Sorbent Injection System please feel free to connect us!
Simply state your requirements and the challenges. Stratgem will provide a solution that will suit your process needs while maintaining product integrity and safe operations.
StratGem
Powder Handling Automation Solutions
StratGem
Powder Handling Automation Products
Plan to Start a Project